The efficiency and productivity of a greenhouse operation is largely dependent on the type of growing structure used. Since there are many designs to select from, it is important to become familiar with the advantages and disadvantages of each. The following is a brief discussion of commercial greenhouses and their structural components.
Types of Greenhouses
Generally speaking, there are three types of greenhouses: lean-to, detached, and ridge and furrow or gutter connected (Figure 1). Few lean-to greenhouses are used for commercial production because of limitations in size. This type of house is the most popular among hobbyists.
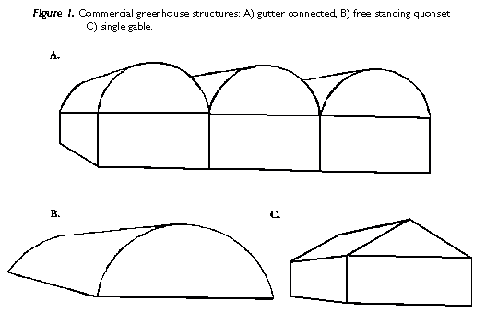
Figure 1. Commercial greenhouse structures: A) gutter connected, B) free standing quonset, C) single gable.
Detached greenhouses stand independently from one another. However, they may be connected to a work area or access another greenhouse through a corridor. The most common type of detached greenhouse for commercial production is the Quonset. These houses are constructed from arched rafters and usually have solid end walls for additional support. Quonset greenhouses are suitable for the production of most crops, but the growing area is somewhat restricted near the side walls. This reduces efficiency as well as productivity.
Ridge and furrow greenhouses are connected at the eave by a common gutter. Generally an internal wall below the gutter is not present allowing for increased efficiency. Ridge and furrow greenhouses may be gabled or curved arch. Gabled houses are usually suitable for heavy coverings (i.e. glass, fiberglass) while curved arch houses are covered with lighter materials (i.e. polyethylene, polycarbonates). Several connected ridge and furrow greenhouses are often referred to as a “range”.
Structural Components
Rafters are the primary vertical support of a greenhouse (Figure 2). They are generally placed on 2, 3, or 4 foot centers depending on strength requirements. Rafters may be of the truss type, or curved arch depending on the width of the greenhouse. Generally speaking, greenhouses over 50 feet wide require a reinforced truss construction.
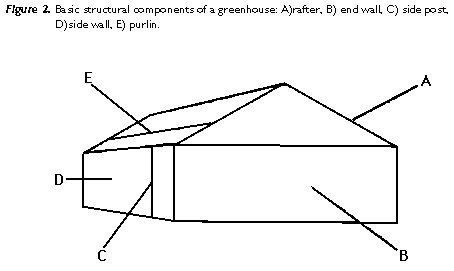
Figure 2. Basic structural components of a greenhouse: A) rafter, B) end wall, C) side post, D) side wall, E) purlin.
Purlins are horizontal supports that run from rafter to rafter. These structural components are usually spaced 4-8 feet apart depending on the size of the greenhouse. Purlins may sometimes be connected by a cross tie. These provide additional support and may be required in areas where high winds are frequent.
Side posts and columns are vertical supports usually ranging in height from 1-10 feet. These structural components deter-mine the height of the production area and greatly influence efficiency. Sidewalls may also be vented to provide cooling and insulation.
Framing Materials
Greenhouses may be constructed from several different materials. Among the most popular are aluminum, steel and wood. Of these three, aluminum is by far the most economical and longest lasting. Aluminum may be extrude in various shapes and thicknesses. This material can then be formed into rafters, side posts and other structural components.
Wood is less commonly used because it deteriorates quickly in the moist environment of the greenhouse. If wood is used, it is best to obtain pressure treated lumber that “resists” decay. There are several satisfactory types of this treated wood available commercially. PENTA, however, has been found to give off fumes that can be harmful to plants.
Covering Materials
Greenhouse coverings must be clear enough to provide optimum light transmission and at the same time be durable as well as economical. Several materials have been developed to meet these needs on a commercial basis.
Glass provides the best light transmission for greenhouse production. However, the structural components required to support glass are costly. Also the initial investment as well as the necessary maintenance has restricted the use of glass houses by Texas producers.
Fiberglass is another covering material that is frequently used on commercial greenhouses. Fiberglass is ridged, extremely durable, and does not require the extensive structural components of a glass house. Unfortunately, fiberglass is very susceptible to break down by ultra violet (UV) light. This causes the fibers to swell resulting in a significant decrease in light transmission. The life span of fiberglass can be as short as five years under certain conditions.
Double sheets of polyethylene (PE) film, inflated with air, is the most common covering on commercial greenhouses in Texas. PE is not rigid, but will provide the support necessary for normal operation. Most currently available PE film will last for approximately two years before it needs to be replaced. Although this frequent maintenance is costly, the reduced initial investment required, as well as the limited structural components needed to support this covering, has made PE most economical for producers.
Several new polycarbonate and acrylic materials are now made for greenhouse coverings. However, at this time there is not enough information available to determine whether they will “out perform” currently used materials.
Summary
The efficiency and productivity of a greenhouse structure is greatly influenced by its design. Also, the initial and long term costs of the facility are effected by the type of materials used. Ridge and furrow houses provide the greatest efficiency in crop production. Aluminum is the most durable and commonly used framing material for commercial greenhouse structures. Double sheets of polyethylene film is the most economical covering material available for Texas producers.