Heating is a major concern to commercial greenhouse producers. This is due primarily to the costs involved in the purchase and operation of heating equipment as well as the potentially disastrous effects of a poorly designed system. Although solar energy represents a significant factor in greenhouse heating, supplemental systems are a necessity for year round production.
Sources and Methods of Distributing Heat
Coal, oil and gas are the most common forms of energy used for greenhouse heating. The choice of which of these to use is based primarily on economics. In Texas gas is the most readily available, as well as economical.
Gas burns efficiently, but all forms must be vented to avoid toxic fumes. Many types of gas heaters have been designed for use in greenhouses and they too effect efficiency. When selecting this type of heating equipment it is important to consider fuel and cost factors.
Heat from gas units may be distributed in several different ways. Perhaps the most common method used is through polyethylene (PE) vent tubes. These PE tubes are generally attached near the heater and are inflated when the blower fan is turned on. The heat is forced through the tube and distributed into the house from holes perforated in the PE. These systems may also be used in combination with ventilation and circulation equipment.
The arrangement of PE tubes in the greenhouse greatly influences efficiency as well as plant growth. When tubes are hung overhead, heat is more likely to move out of the “plant zone” and into the upper portion of the structure. When tubes are placed under the benches efficiency is improved and heat is maintained in the appropriate area for optimum plant growth. This type of tube arrangement requires floor mount heating systems or ducts that move the heat from overhead units to the under bench tubes.
Although boilers and traditional hot water/steam heating systems are not used extensively in this area, there is a variation of these systems that is becoming increasingly popular among Texas growers. The use of hot water for “under pot heating” has been proven to be extremely effective and efficient. In these systems, water is heated in a modified hot water heater and pumped through an extensive tubing system that is mounted to the bench. The heat is radiated from the tubes and absorbed by the pots that are placed directly on them. The media in the pot is maintained at a constant temperature which allows air temperatures to be held much lower than with traditional systems. The overall effect is improved plant growth and reduced energy costs.
Thermostats and Controls
There are several types of thermostats and environmental controllers that are available for commercial greenhouse production. Regardless of how sophisticated this equipment is, there are some very basic factors that must be considered if the system is to operate properly.
Sensing devices should be placed at plant level in the greenhouse. Thermostats hung at eye level are easy to read but do not provide the necessary input for optimum environmental control. It is also important to have an appropriate number of sensors throughout the production area. Often times environmental conditions can vary significantly within a small distance.
Do not place thermostats in the direct rays of the sun. This will obviously result in poor readings. Mount thermostat so that they face North or in a protected location. It is also sometimes necessary to use a small fan to pull air over the thermostat to get appropriate values.
Calculating Greenhouse Heating Requirements
The key to efficiently heating a greenhouse is matching the equipment to the types of crops to be produced. The first step in this process is to determine the heat loss of the greenhouse. Based on this information the type and capacity of a system may be selected. The following is a series of formulas which may be used for these calculations.
- Using Figure 1, determine the exposed surface area of the greenhouse covering (i.e. poly, fiberglass, glass, etc.).
- Using Figure 1, determine the exposed surface area of other materials (i.e. concrete block, poured cement, brick, etc.).
- From Table 1, determine the corresponding U value for each of the materials listed in 1 and 2 above.
- Determine the difference between the highest temperature to be maintained in the greenhouse and the minimum outside night temperature where: T = (max inside temp) – (min outside temp)
- Calculate the conduction heat loss factor (QC) for each of the materials listed in 1 and 2 where: QC = Exposed surface area x U x T
- Using Figure 1, calculate the volume of the greenhouse structure (V).
- Using Table 2, calculate the air infiltration heat loss (QA) where: QA = 0.22 x T x V x value from Table 2
- Calculate total greenhouse heat loss (QT) where: QT = QC + QA
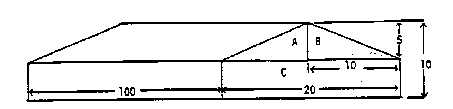
Even Span Structure
Area A and B = ½ (5 x 10) =25
Area C = 20 x 5 = 100
Total Area = A + B + C = 100 + 25 + 25 = 150
Volume = Length x Total Area = 100 x 150 = 15,000 cu. ft.
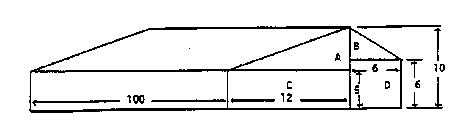
3/4 Span Structure
Area A = ½ (12 x 5) = 30
Area B = ½ (4 x 6) = 12
Area C = 12 x 5 = 60
Area D = 6 x 6 = 36
Total Area = A + B + C + D = 30 + 12 + 60 + 36 = 138
Volume = Length x Total Area = 100 x 138 = 13,800 cu. ft.
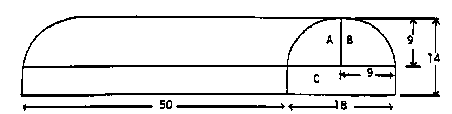
Roundtop Structure
Area A + B = ½ (π r 2 ) = 127 sq. ft.
Area C = 5 x 18 = 90 sq. ft.
Total Area = (A + B) + C = 127 + 90 = 217 sq. ft.
Volume = Length(50) x Total Area (217) = 10,850 cu. ft.
Material | U Value (BTU/(h °F ft²)) |
---|---|
The smaller the U value the lower the heat loss | |
1. Glass, single layer | 1.13 |
2. Glass, double layer,1/4″ space | 0.65 |
3. PE film, single layer | 1.15 |
4. PE film, double layer, seperated | 0.70 |
5. Fiberglass | 1.00 |
6. Concrete block, 8″ | 0.51 |
7. Concrete block, 8″ plus 1″ foam urethane | 0.13 |
8. Concrete block, 8″ plus 1″ foam polystyrene | 0.18 |
9. Concrete poured, 6″ | 0.75 |
10. Cememt asbestos board, 1/4″ | 1.10 |
11. Cement asbestos board, 1/4″ plus 1″ foam urethane | 0.14 |
12. Cement asbestos board, 1/4″ plus 1″ foam poly styrene | 0.21 |
Construction System | Air Exchanges per Hour |
---|---|
Low wind or protection from the wind reduces the air exchange rate | |
1. New construction, glass or fiberglass | 0.75 to 1.5 |
2. New construction, double layer PE | 0.50 to 1.0 |
3. Old construction, glass, good maintenance | 1.00 to 2.0 |
4. Old construction, glass, poor condition | 2.00 to 4.0 |